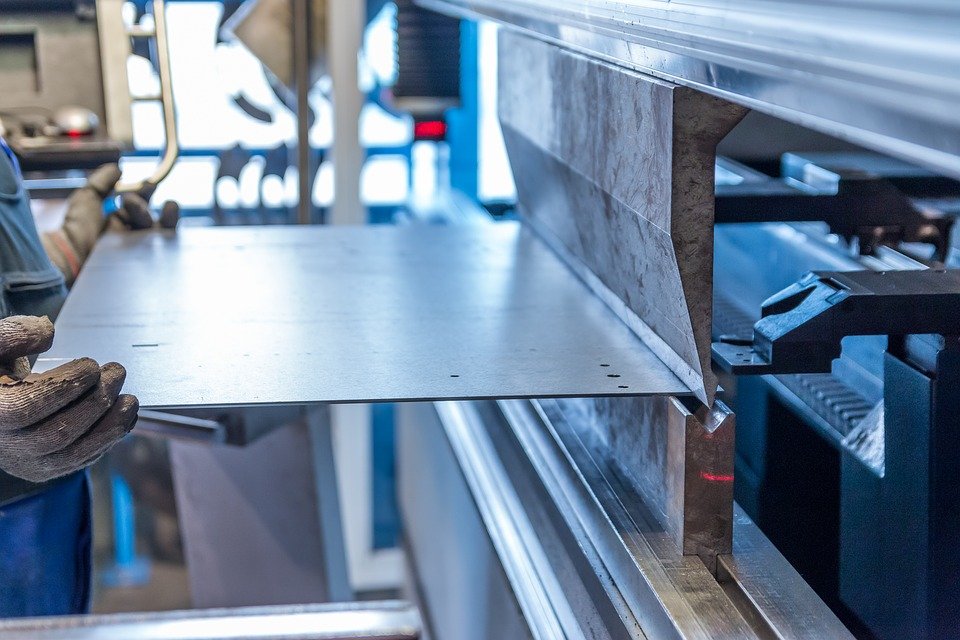
Sheet metal manufacturing involves forming different materials into useful constructions. Sheet metal is used to build all kinds of home structures as well as industrial ones. There are various types of sheet metals and each has its own applications. Metal is used for constructing ships, buildings, bridges, tanks, car parts, and all sorts of other things.
Most common metals that are used in Sheet metal fabrication are steel, aluminum, tin, and iron. These are the materials most often used for making all kinds of home structures. Some other common materials that are incorporated in sheet metal fabrication are plastics and wood. Wood and plastics are generally used in home structures because they are easily formed into the different shapes needed.
Sheet metal is used extensively in the automotive industry. It can be made to create the front fenders and the bumpers for vehicles. Automakers are able to save a lot of money when using metal in their products. The metal is also used extensively in the construction of motorcycles. In fact, sheet metal fabrication is so important in the motorcycle industry that many manufacturers prefer to use metal instead of steel when building motorcycles.
When sheet metal is used in airplane construction, it is important that it is lightweight and strong. Because the airplane needs to travel fast, it is crucial that the aircraft is lightweight and the fuel efficient as possible. Engineers have found great uses for lightweight metal in making aircraft. For instance, they are able to make the airframe of an airplane much more aerodynamic by designing hollow sections that are hollow from the very start. These sections are called flaps and they can make the plane much lighter without having to sacrifice the structural integrity.
The sheet metal manufacturing process produces a variety of different products. They are commonly made for automobiles, but they can also be used to make all kinds of jewelry. You may have seen some jewelry pieces made from old gold earrings. This is a great way to get a stylish item at a cheap price without spending too much. The same is true for other precious items. For instance, an old coin can be turned into a very valuable piece of jewelry when it is remade from sheet metal.
In the past sheet metals were mostly machined using large machines, but modern day sheet metal manufacturing techniques are allowing smaller machines to perform some of the same tasks. This is because they generally are designed to work more quickly. Check it out here for more information about the process of metal sheet fabrication.
Some of the smaller sheet metal manufacturing machines include compactmakers, saws, wire brushes and even robotic welders. The uses for this equipment are nearly limitless and nearly every company that uses sheet metal manufacturing in their products would be unable to do them without the help of these machines. To get more enlightened on the topic, check out this related post: https://en.wikipedia.org/wiki/Metalworking.